Reusable industrial wipes: 3 ways they will improve your business
Cleaning cloths
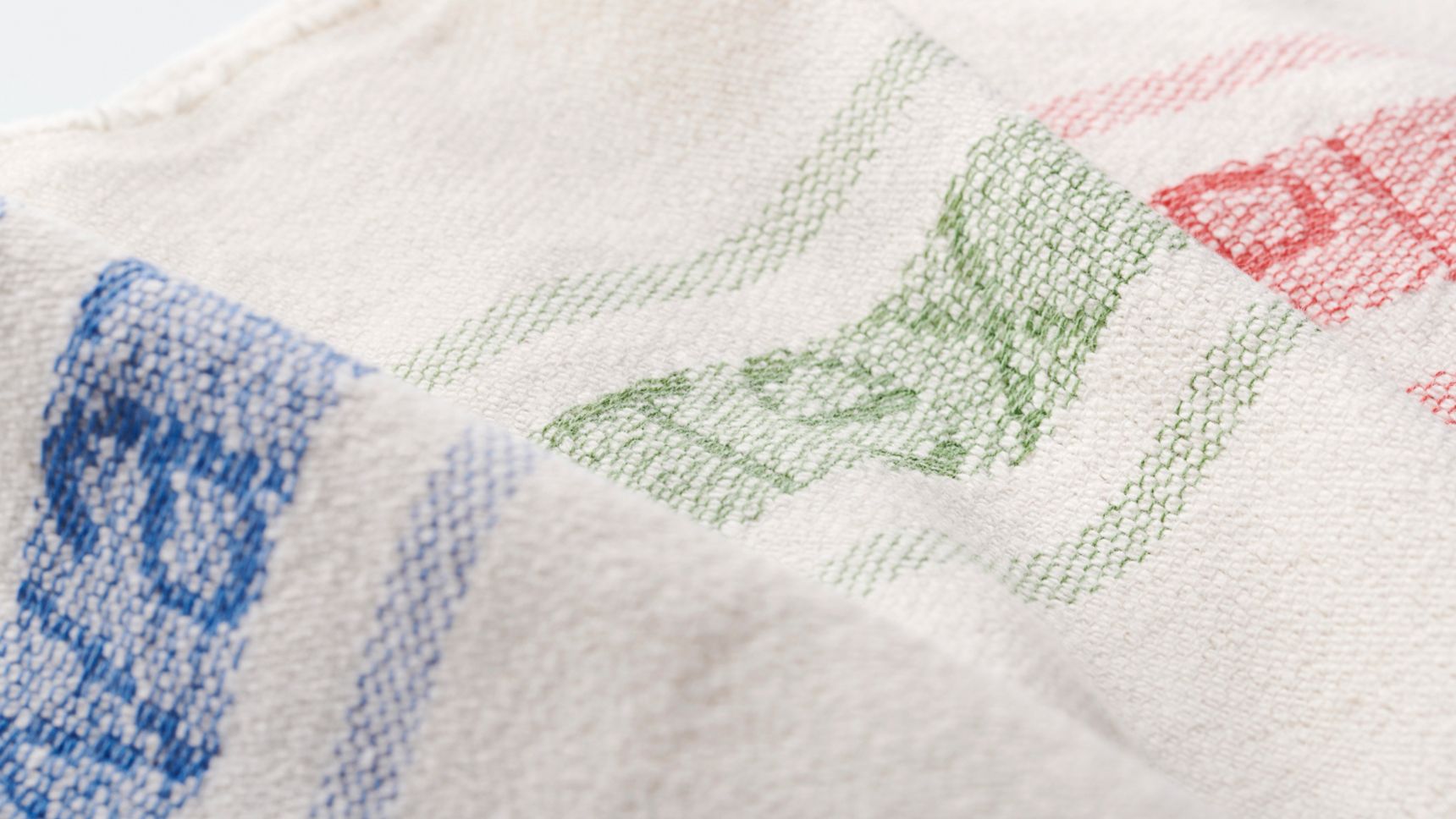
The sharing economy is booming with more consumers ‘using instead of owning’ – think Airbnb or Zipcar. And it’s increasing amongst the business community too. Such collaborative consumption – the shared use of a good or service by a group – has been at the heart of the Mewa business model for over 100 years with its circular reusable industrial cleaning cloth system and is now used by 190,000 companies across 21 countries.
The concept is simple; cleaning wipes are delivered in a dedicated safety container, the cloths are used and stored in the safety container, then picked up, washed, dried and recirculated.
This model for cleaning wipes has become the common standard across Europe, especially within the automotive, printing and industrial manufacturing sectors. In fact, every day 2.7 million people use MEWA wipes in their work. And so great is the demand for MEWA wipes, that we weave 5 new cleaning wipes every second in our weaving mill – that’s 113 million new pieces a year.
Why are Mewa wipes so popular? We look at some of ways your business will benefit with our end-to-end full-service leasing model.
1. Increase productivity
Mewa cleaning wipes are made from high quality cotton, are extremely absorbent and able to soak up large volumes of liquids fast. In fact, they can absorb large volumes of oil and other liquids. Compared to disposable paper rolls, our cloths save up to 30% on cleaning times.
Our absorbent mats too can absorb an incredible 3 litres of fluid such as oils, solvents and other liquids, transporting the fluid from the outer fabric into its special fibre core, keeping the surface dry. This eliminates the need for drip trays or oil pans and granules or sand to soak up these liquids, all of which are time consuming to administer.
Time and cost efficiencies
The Mewa leasing system eliminates unnecessary administration and management time too. The right number of wipes or oil trapping mats are delivered to your door for when you need them and security of supply is guaranteed.
There’s no need to keep checking stock, re-ordering supplies and raising purchase orders, not to mention finding somewhere to store the wipes. And you will always have full control of costs and won’t be tying up capital either.
Storage of used wipes and mats in our SaCon safety container also reduces your overall storage and disposal costs as well as mitigating potential health and safety fines.
2. Boost your environmental credentials
Running your business in a way that’s good for the environment is a key selling point for your customers. Research shows that sustainability and ethical business practices are things that people really care about and will help companies attract and retain customers and the best talent.
Mewa wipes are a cost effective and sustainable alternative to single-use products such as paper wipes. A single Mewa cloth can be reused up to 50 times. We estimate that each year, the use of our wipes and mats by our customers prevent the generation of significant amounts of industrial waste.
Less waste and energy use
Independent studies have shown that the consumption of resources when using disposable cleaning materials is five to eight times higher than a reusable principle.
Green your supply chain
As well as improving your direct environmental impact, partnering with Mewa will help you to green your supply chain too. If you take your environmental responsibility seriously, you can’t do one without the other.
For good reason, nearly a quarter of a century ago, we were the first company in our industry to be awarded the International Environmental Certificate in accordance with ISO 14001 and we continue to lead the way.
Through innovation and investment we employ environmentally friendly production processes including heat recovery, thermal utilisation of residual materials, wastewater treatment and raw material recycling.
Specifically:
• We recover the oil and fat content from dirty cleaning cloths to power our washing and drying systems covering up to 80% of our energy requirements;
• Heat recovery from our washing and drying systems heats the water for our washing processes, saving around 7 million litres of heating oil a year;
• By recycling our rinsing and washing water, water consumption is 50% less compared to a conventional process;
• Our wastewater treatment achieves a 99.8% degree of purification;
• Precise dosing equipment and using biodegradable washing cleaners means up to 85% less pollution compared to conventional processes;
• Cotton lint produced during the manufacturing of our wipes is turned into insulating material.
3. Improve your health & Safety
Health & Safety compliance is a headache and a worry for most companies, especially smaller ones that may not have dedicated health and safety staff.
A wide range of fluids, such as oil and other lubricants, hydraulic fluids and solvents, are employed in industrial environments meaning leaks and spills are a regular occurrence. Furthermore a lot of these liquids come with environmental and health and safety hazards and correct disposal is tightly regulated.
Reduce workplace hazards
The UK Health & Safety Executive (HSE) recommends that spills of liquids are promptly addressed to reduce the risks of exposure to hazardous materials and also reduce the risk of slips and trips.
HSE figures show that slips and trips are the most common cause of major injuries at work. 95% of major slips result in broken bones and, on average, are responsible for 20% of over-three-day injuries to employees. The cost to UK employers is £512 million a year in lost production and other costs.
Frequent and prolonged contact with fluids such as solvents and used oil may also cause dermatitis and other skin disorders, including skin cancer.
As such, it is incumbent on the owners and managers of industrial sites to prevent spillages of fluids, provide suitable materials for cleaning-up spills when they do happen and for ensuring that spills are cleaned-up immediately.
Commonly though businesses take a ‘one-size-fits-all approach,’ using traditional rags and paper rolls to clean up oil or chemical spills as well as to remove metal filings, wipe down machinery, clean hands and more. Unfortunately, these types of wipes lack absorbency and any specialty for the job in hand, making them inferior tools for good health & safety compliance.
Dispose of hazardous waste safely
Any cleaning cloths soaked with oil, and many other industrial fluids, are classified as “absolute hazardous” entries on the Waste Framework Directive’s “List of Waste” document.
Therefore, to ensure that you remain compliant with legal regulations, all wastes contaminated with absolute hazardous industrial fluids, including any cloths used to mop-up spillages, must be safely stored in a suitable recipient such as the Mewa SaCon safety container, before being disposed of by an accredited hazardous wastes contractor.
Peace of mind
The business of keeping factory and workshop floors and industrial machinery clean and storing and disposing of hazardous waste should be a top priority, but managers face many other demands on their time.
With the Mewa approach you will have peace of mind that you are health & safety compliant.
• The right cleaning wipe for the job; a choice of absorbency levels and lint content for non-sensitive and sensitive surfaces. • Oil-trapping mat; super absorbent mat providing a simple and efficient way to keep the workplace and floor free from contamination and hazardous fluids. • Safe and hygienic storage; our SaCon safety container means soiled wipes and mats, including those containing hazardous waste, are stored and dealt with safely and meet legal regulations.
Get the Mewa benefits for your business
Find out more about how Mewa can improve your productivity, environmental credentials and health and safety compliance.
Get in touch to set up a product trial or request a demonstration at your premises from one of our dedicated technicians, so you can compare our solution to your current system.
Pictures and film material
Press Contact
4CM Ltd
Liz Menches liz.menches@4cm.co.uk
Challenge House Sherwood Drive Bletchley Milton Keynes MK3 6DP